The ABCs of Custom Carving Knives - Advice from the Pros
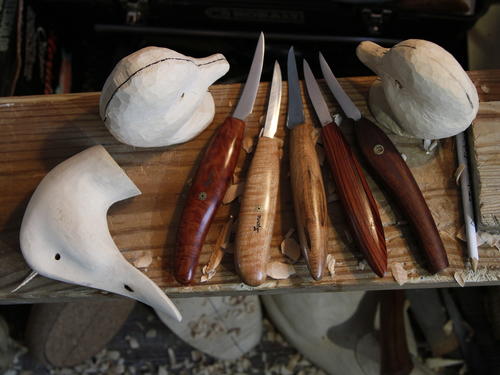
A few years ago at the Ward World Championship in Ocean City, Maryland, I watched Ashely Gray do a knife demonstration. He used a big, long tupelo knife in a way I had never seen before. Once he finished, I set off to visit the knife vendors at the show and get myself one of those long knives. As I browsed the vendor booths, I felt a bit like a kid at a candy store. Not only did I get to see all the different knives, but I also got to see how carvers used some of them.
In the first part of this article (Winter 2016), I discussed how custom knives are manufactured and demonstrated the basic cuts. In this part, I’ll share the viewpoints of several top carvers. I had my work cut out for me (pun intended) trying to find bird carvers who use knives. Most of the ones I approached use Foredom tools to remove the bulk wood and some micromotor tool for fine detail. All the carvers I interviewed agreed that knives usually offer better control of the amount of wood you remove. It also is a more relaxing carving method, and is obviously a lot quieter than running a power grinder.
This article was featured in the Spring 2016 issue.
Read NextThe Tease of the Teasel